Savoir-faire: warp printing
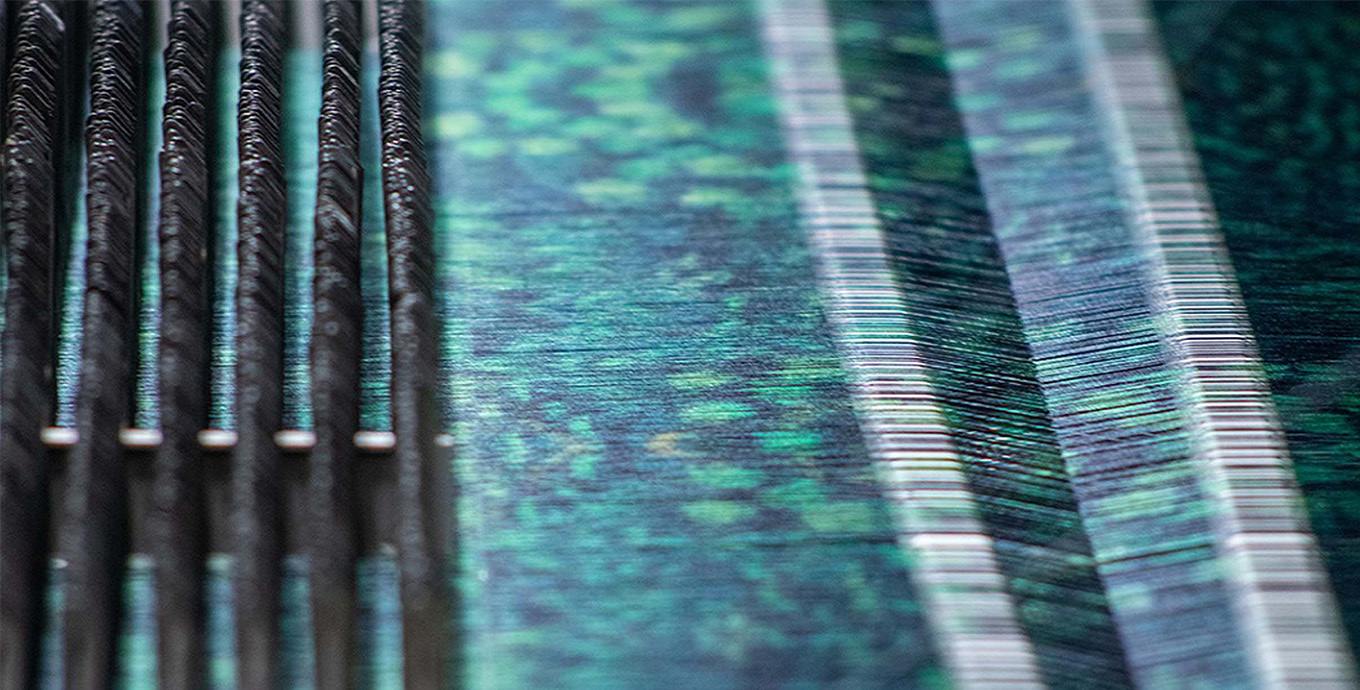
Dating back to the early 19th century, warp printing is a technique that has its origins in the Indonesian Ikat dyeing process. It is a craftsmanship that combines the art of printing with that of weaving, resulting in a motif with characteristic shaded traits. Also known as chiné or chiné à la branche, the technique became popular in the second half of the 19th century in Europe, particularly at the French court, which was fascinated by the exoticism of Oriental designs and textiles. Today, the printed chain is used by craftsmen and experts who collaborate with Dedar to create fabrics that combine expressive and textile savoir-faire.
This meticulous process begins with the printing of the pattern on the warp threads, before weaving. The threads, carefully and precisely positioned between two cylinders, are pressed at a temperature of 180 degrees: thanks to the heat, the pattern is transferred onto the yarns. The warp is then placed on the jacquard looms and woven into a double weft: one fine and bright, the other consisting of a thicker yarn. From the weaving of the two wefts with the printed warp yarns, the pattern is defined, giving shape to Nenufar, a garden populated by water lilies, with a pictorial stroke, vibrant in its contours and precious in its technique. | Photo credit: Giulio Ghirardi
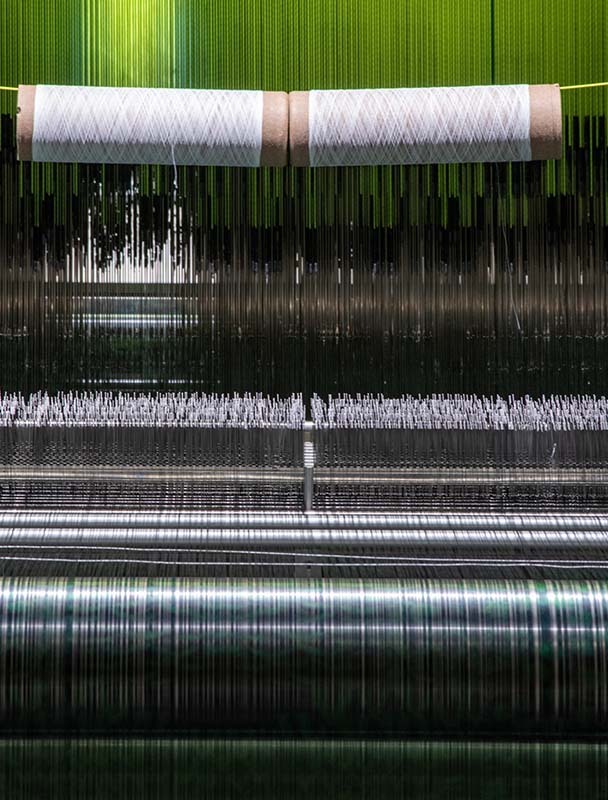
The printed warp yarns are carefully positioned on jacquard looms.
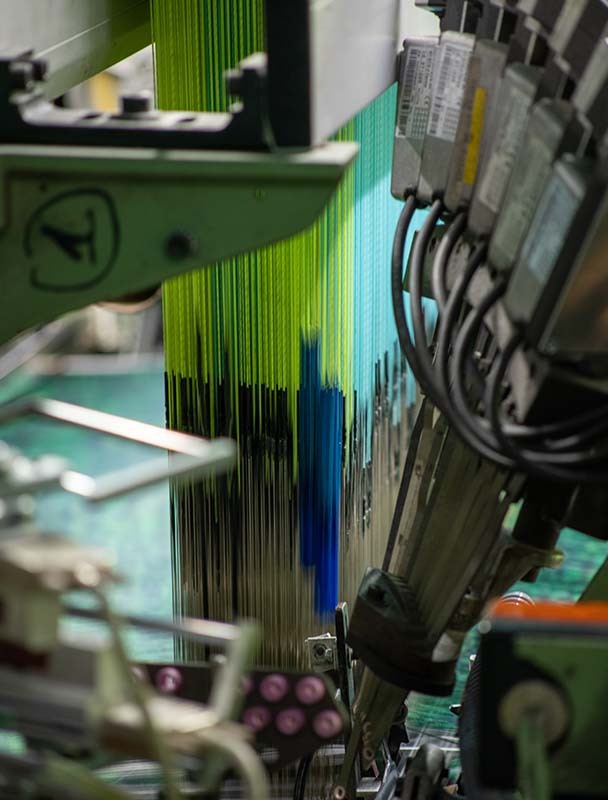
A double weft is prepared for weaving.
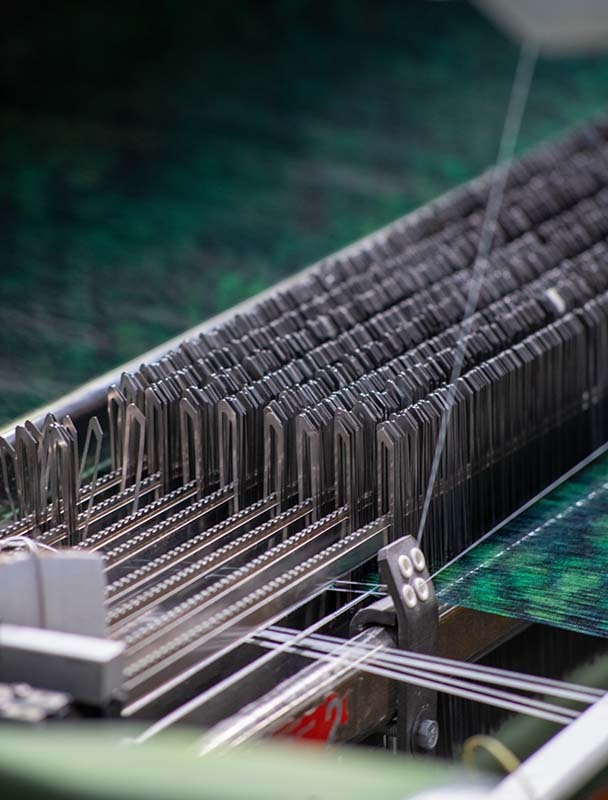
Warp and weft yarns intertwine on jacquard looms.
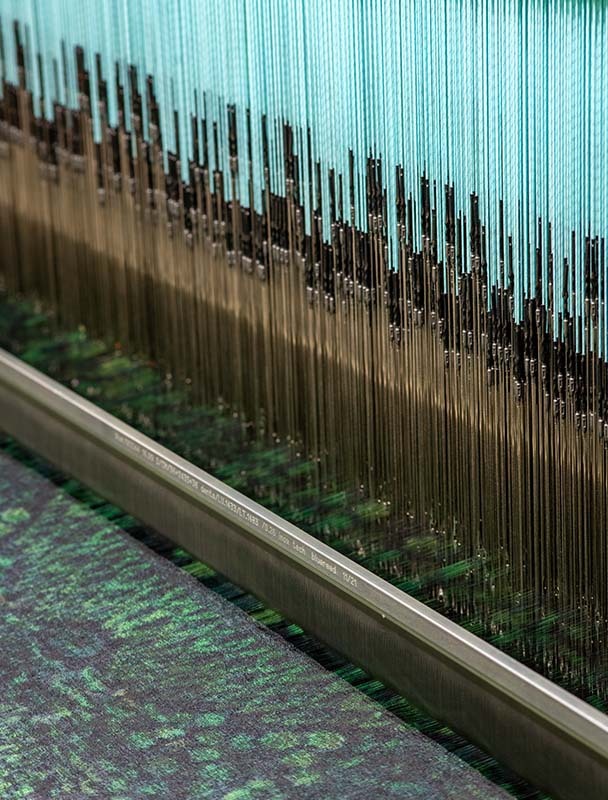
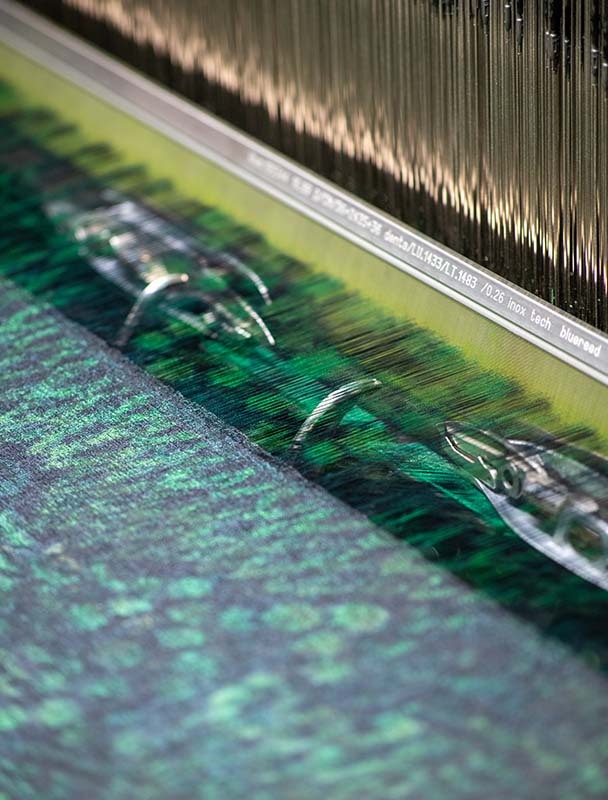
The heddles rhythmically move the warp yarns.
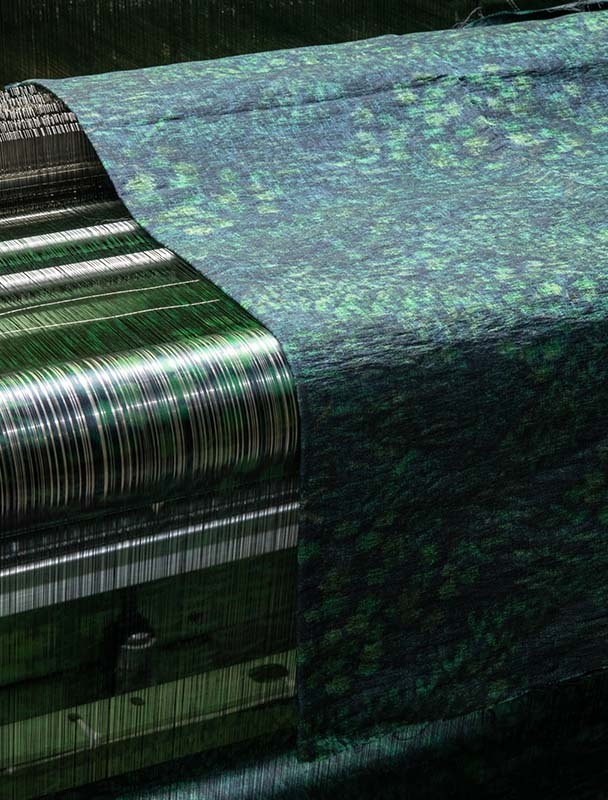
Nenufar pattern takes shapes.
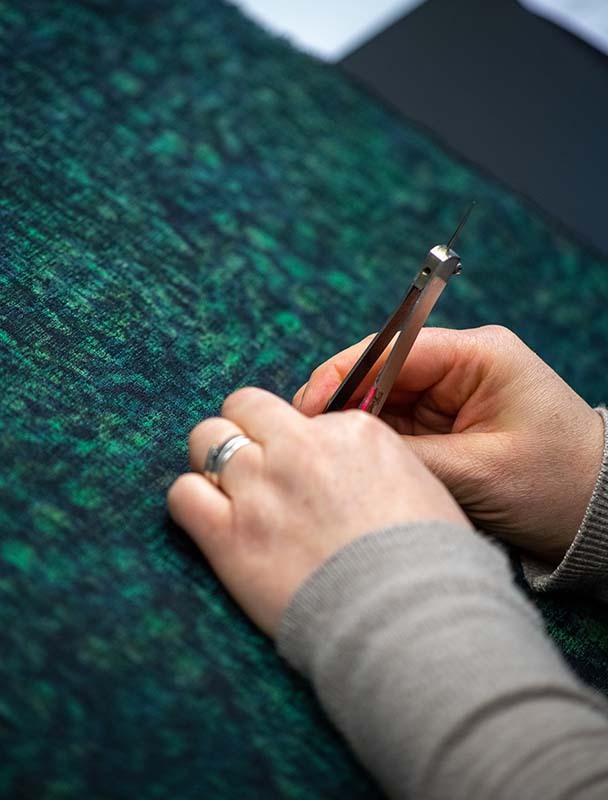
The expert hands of the craftsmen perfect the fabric.
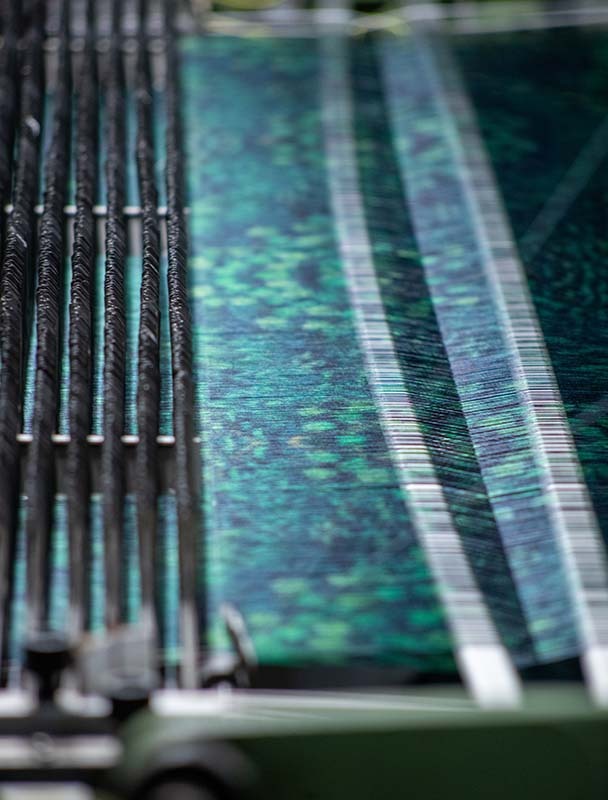
The impression of a garden emerges through meticulous expertise.